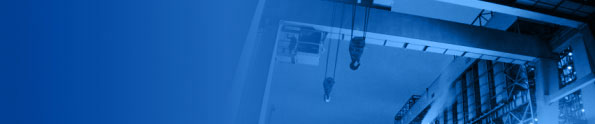
ATop
Absolute accuracy
Absolute accuracy means the maximum difference between target position (ideal position) and current position for each measurable position within the measuring range. In practical use, the resolution of positioning systems most often is far better than their absolute accuracy which is limited by reverse tolerance, hysteresis, drift, non-linearity of drive or measuring system, tilt, etc.
Absolute singleturn encoders
Encoders providing a clearly coded information for each individual measuring step within one turn. The data remain available even after power interruptions.
Absolute multiturn encoders
Encoders capable of capturing additionally to the singleturn count data also the number of turns. The data remain also available after power interruptions and moreover the encoders continue capturing the turns even in powerless state.
AC (~)
Supply voltage as alternating current.
Accuracy
Deviation between true and measured position.
Ambient temperature (EX design)
Temperature during device operation.
ASI
Asynchronous serial interface. Serial transmission bound by data protocol. Driver hardware according to EIA RS485.
ASIC
Application specific IC.
ATEX
Since July 1st, 2003 any electrical appliance put into circulation for application in EX-areas must be in line with ATEX standard 95/9/EG.
Antivalent output / push-pull
Depending on the wiring, the output can be defined as NO (normally open) or NC (normally closed). Both output options are available at the same time.
BTop
Baud rate
Transmission rate in bits per second with serial interfaces.
Binary code
The code structure is similar to the decimal count system, however only „0“ and „1“ are known as figures.
Bit / byte
One bit (binary-digit) is the smallest information unit in the binary system, one byte consists of 8 bits.
CTop
CAN-Bus
Multi-master-bus system on 2-wire line. The system is operating event-triggered respectively remotely requested. At present, standardized CAN protocols are being specified as CANopen.
CE mark
Approved conformity to EC-requirements regarding immunity against electromagnetic interference (EMC), emitted interference and low-voltage standards.
Clock+, clock-
SSI interface control lines for synchronous data transmission. Clock+ together with clock- form a current loop for non-potential takeover of the SSI encoder clock frequency.
Clock frequency (SSI)
Clock frequency of absolute encoders with synchronous serial interface (SSI) means the clock signal frequency during data transmission. Applicable clock frequency is defined by downstream electronics.
Code sequence
The code sequence is defining the rotating direction for the output code in ascending values.
Code switching frequency
Number of measured steps per second at absolute encoders. For encoders utilizing a 13 bit resolution and 800 kHz code switching frequency the maximum electric rotation speed is 6000 rpm.
CSA approval
Approved by Canadian Standards Association.
Counting direction (UP/DOWN)
Control input for definition of data output sequence, ascending with clockwise or counterclockwise shaft rotation.
Coupling
The most appropriate kind of coupling can be traced by referring to the data of the drive system. Resolution, acceleration as well as the required positioning accuracy have to be taken into consideration. An estimate of the possible dragged angle can be made with regard to torsion stiffness. With highly dynamic drives however the torque often is substantial. To get an idea of the torque and resonance vibrations the product data sheet gives information on the moment of inertia.
Current consumption
Max. circuit current consumption at nominal voltage (without load).
cw / ccw
Clockwise / counterclockwise when looking at flange.
DTop
Datavalid (DV)
Diagnostic output for validity check of the output data.
DC (=)
Supply voltage as direct current.
Decimal BCD code
To avoid a decimal number having to be converted into a binary number most often not the natural binary code is utilized but instead the individual figures of the decimal number are coded in the binary way.
Describing files
EDS - (Electronical Data Sheet) provides the device-specific parameter significance for CANopen and DeviceNet appliances.
GSD - (device master file) provides the device-specific parameter significance for Profibus appliances.
XML - (Extensible Markup Language) provides the device-specific parameter significance for EtherCAT- appliances.
Diagnostic functions
The encoders are subject to permanent monitoring regarding any malfunction. Upon occurring a code disc error, scanning error or power failure for example a corresponding error warning will be given.
ETop
E-connection-cable
For encoders with connector output the corresponding mating connector is available as accessory. Encoders with cable output are available with standard cable length of 2, 5 or 10 m. Coating isolation is made of PUR. The cable shield is normally provided by housing respectively flange mount.
EMI (EMC)
Electromagnetic interferences/compatibility. European standards 89/336/EWG define basic uniform requirements on electromagnetic compatibility (emitted interference and interference immunity). The European standard DIN EN 61000 is defining concrete requirements.
Enable
Control input to activate data outputs of absolute encoders with parallel interface.
End shaft Non-through hollow shaft or blind shaft. Encoders with end shaft provide the same mechanical characteristics as shaft encoders but nevertheless enable mounting by clamping ring and spring washer like a hollow shaft encoder. Hollow shaft encoders with non-through hollow shaft are mounted by face center screw.
Error limit
Error limit means the maximum deviation of all measured values from the target taking as reference a standard of one turn of 360° covering the complete operating temperature range.
Explosion protection standard
Approval for encoder application in explosive areas certifying the special encoder protection in line with corresponding standards.
FTop
Fiber-optic
Cable made of glass or plastic fibres to transmit the light emitted by an opto-electronic sensor.
GTop
Gray code
The gray code is a one-step code utilized by most absolute encoders. A symmetric cut gray code is a defined cutout off the complete gray code. Thus, there is always an even number in graduation of steps.
ITop
Impulse number
The impulse disc, for example of glass, provides a defined number of line markings. These markings are scanned by a beam of light inside the encoder in order to evaluate the number of impulses, i.e. the resolution
Impulse tolerance
The tolerance for the impulse period ratio is ±10%. Regarding any deviations there are special remarks on the respective product data sheet. This close tolerance applies also for the two impulse tracks A and B shifted by 90° in order to guarantee at any time a true recognition of the rotating direction or the true electronic impulse multiplication.
Initializing time
Reaction time after power on.
Incremental encoder
Encoder emitting an electrical impulse (High/Low) for each measuring step.
Interpolation
By help of electronics and applying trigonometrical formulas the base period is devided into inferior units enabling a multiplication (interpolation) by 10 of the basic resolution.
Interface RS232
RS232 full-duplex transmission, properties:
- Asymmetrical
- 3 lines
- Point-to-point connection
- 1 transmitter and 1 receiver
- Data transmission line: max. 30 m
Interface RS422
RS422 full-duplex transmission, properties:
- Asymmetrical
- 4 lines
- Multipoint connection
- 1 transmitter and 32 receivers
- Data transmission line: max. 1500 m
Interface RS485
RS485 full-duplex transmission, properties:
- Asymmetrical
- 2 lines
- Multipoint connection
- Transmitter and receiver (max. 32 devices)
- Data transmission line: max. 1500 m
Interference immunity / emitted
Refer to EMI.
LED
Light emitting diode.
LTop
Limit frequency
The following formula is applicable for calculation of the max. rotation speed in relation to the encoder impulse number resp. step number. The maximum rotation speed must not exceed the mechanical rotation speed limit. fmax = (rotation speed x impulse number) / 60.
MTop
Magnetic field sensor
Magnetic encoders capture the angle by touchless sensing of a magnetized pole wheel by help of a magneto-resistive sensor.
Magnetic encoder, linear
Linear magnetic field sensors are especially recommendable for incremental capturing of displacements over a medium distance. They offer resolutions of <20 micro meters.
Max. load current
Defines the max. permitted current put on the output without any time limit.
Measured step
The smallest measurable angle.
Measured step deviation
Refer to accuracy.
Multiturn encoder
Encoder capturing in addition to the singleturn count data also the number of turns. The information remains available also in case of power interruptions when the encoder continues capturing the turns.
NTop
NC
"Not connected", output not assigned.
NPN
Digital output triggered to minus. The load is between the output and +UB.
Number of steps
A glass impulse disc provides a certain number of line markings that are scanned inside the encoder by a beam of light, thus defining the possible resolution (number of steps).
OTop
Output
Output means the electric output signal generated by the sensor. It can be either digital or analog.
Operating current
Refer to current consumption.
Operating temperature
Ambient temperature together with device-specific electronic and mechanical warming.
Operating torque
Force required for keeping the shaft turning at a specified rotation speed.
PTop
Performance driver
Do not confuse with linedriver.
PNP
Digital output switching to plus. The load is between output and GND.
Preset
The current output value of an absolute encoder is being overwritten by the preset.
Profibus-DP
Master-slave-bus-system on 2-wire line. Line bus utilizing EIA RS485 hardware interface. Standardized Profibus-DP protocol for encoders.
Protection classification (IEC 60529)
Protection classifications define the scope of protection of a machine or sensor against contact and penetration of soiling particles and water. The standard name starts with the letters IP followed by a two-digit number. The first digit represents the protection against contact and penetration of soiling particles. The second digit defines the protection against water penetration. The higher the number, the higher the respective protection. In the industrial sector so far protections up to IP 65 have prevailed as standard.
Protection standard
Protection standards (EN 61010) define corresponding protective steps against electrical shocks.
PTB approval
German Federal Physio-Technical Institute. Approved mechanical or electronic meter counters for calibrated length measurement. Counters with PTB approval can be applied for calibrated length measurement after having had approved the entire measuring system.
RTop
Resolution
The resolution of singleturn encoders means the number of steps per turn. The resolution of multiturn encoders provides the number of steps per turn and the number of turns.
Resistance
Refer to shock and vibration.
Repeatability
Repeatability (according DIN 32878) means maximum scattering of the measured values within at least five deviation diagrams recorded subsequently in one rotating direction at a defined temperature.
Repetition accuracy
Deviation between two subsequent measuring operations at a defined object under identical conditions.
Reverse polarity protection
Most sensors provide protection against reverse polarity and reverse voltage. Any incorrect connection will not lead to destruction.
Rotation speed
The mechanically permitted rotation speed depends on the applied ball-bearing and should not be exceeded. The max. electrically permitted rotation speed is determined by the limit frequency of the integrated electronics respectively of the downstream electronics.
Ripple residue
Max. share of AC ripple in DC voltage supply. Value defined in % of average +UB.
STop
Scaling
Customer-specific designation of encoder resolution. The encoder calculates the resolution requested by customer by help of the basic resolution and scaling factor.
Shaft load (permitted)
Permitted shaft load means the maximum force applied on the shaft without impacts of failure or reduction of the bearing service life. It is devided into axial and radial shaft load.
Shock and vibration
Resistance of the Hesmor encoders against shocks and vibration is subject to type-specific tests in line with standard DIN EN 60068-2-27 (shock) respectively standard DIN EN 60068-2-6 (vibrations).
SSI
Synchronous serial interface. Serial data transmission bound to external clock.
Starting torque
Starting torque means the initial force required for making an idle shaft rotate.
Store
Control input by help of which the data outputs of absolute encoders are stored for save readout. It is recommended to use the store input especially with multistep data codes (binary code).
Supply voltage range
Permitted supply voltage range for encoder operation.
TTop
Torque
The torque has to be kept as inferior as possible since sensors must not put any load on the drive. The encoder torque is depending on size and type of ball-bearing, ball-bearing grease, operating temperature, mechanical rotation speed and many other factors. In general, the slower the rotation speed resp. the smaller the shaft diameter and the inferior the shaft protection class, the less the torque.
Total resolution
Total resolution of singleturn encoders means the number of measured steps per turn. Total resolution of multiturn encoders means the number of measured steps per turn multiplied by the number of turns.
UTop
UL-approvals
Products with UL approvals are subject to specific tests on their characteristics under consideration of some kinds of danger and appropriate use under certain prevailing conditions. Insurance as well as regulating authorities and consumers in the USA and Canada meanwhile do no longer accept any other certificate.
VTop
VAC
Refer to AC.
VDC
Refer to DC
ZTop
Zero point setting
Control input for setting the zero point anywhere within the absolute encoder resolution range without mechanical adjustment. At programmable absolute encoders the option „zero point setting“ enables also setting an offset.
Zero signal / reference signal
Zero pulse of an incremental encoder that is output once on 360°.